Lubrication is the lifeblood of a Formula 1 engine. Operating at speeds exceeding 15,000 RPM and under immense loads and temperatures, an F1 engine relies on its lubrication system to minimize friction, reduce wear, dissipate heat, and ensure reliability. Modern F1 engines utilize sophisticated dry sump lubrication systems and highly specialized oil types, coupled with advanced oil cooling and management strategies. This article explores the technical details of these critical aspects of Formula 1 engine lubrication.
Dry Sump Lubrication: Ensuring Oil Delivery Under Extreme G-Forces
Formula 1 engines almost universally employ dry sump lubrication systems, a departure from the more common wet sump systems found in most road cars. The choice of dry sump is driven by the extreme demands of racing, particularly the high G-forces experienced during cornering and braking.
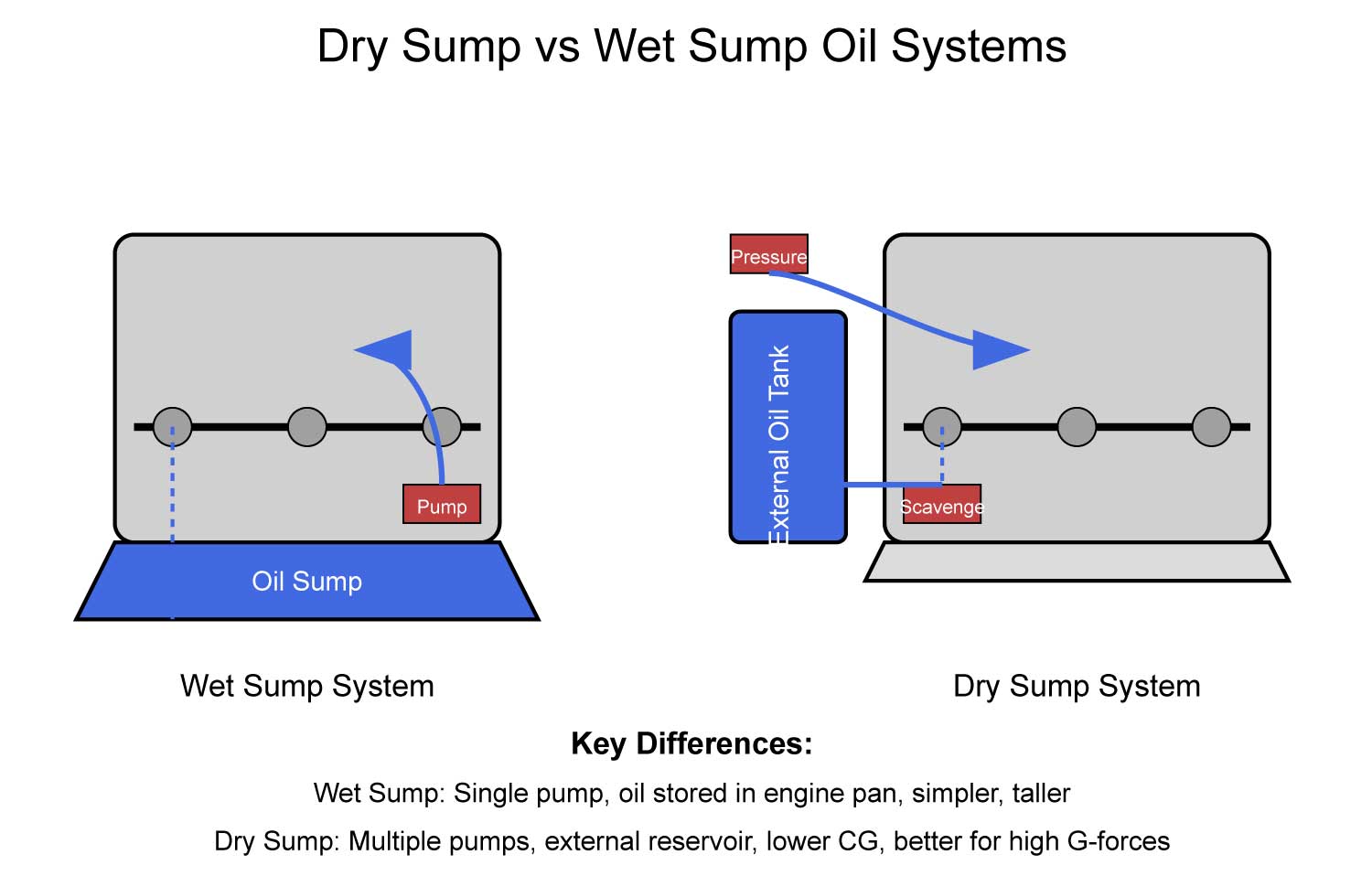
-
Wet Sump vs. Dry Sump - The Fundamental Difference:
- Wet Sump: In a wet sump system (common in road cars), the engine oil is stored in a sump, which is an integral part of the engine block, typically located at the bottom. A single oil pump draws oil from this sump and circulates it through the engine.
- Dry Sump: In a dry sump system, the oil is stored in a separate external oil tank, located outside the engine block. Multiple oil pumps are used:
- Pressure Pump: Draws oil from the external tank and delivers it under pressure to lubricate engine components (bearings, pistons, valvetrain, etc.).
- Scavenge Pump(s): One or more scavenge pumps actively extract oil from the engine's crankcase (the area around the crankshaft) and return it to the external oil tank. This "scavenging" action is key to the dry sump system.
-
Advantages of Dry Sump in Formula 1:
- Prevention of Oil Starvation: During high-speed cornering and braking, G-forces can cause oil to slosh to one side of a wet sump, potentially uncovering the oil pump pickup and leading to oil starvation. Oil starvation means critical engine parts are momentarily deprived of lubrication, which can cause rapid wear and catastrophic engine failure. Dry sump systems, with their scavenge pumps and external tank, prevent oil starvation by ensuring a consistent supply of oil to the pressure pump, regardless of G-forces or car orientation.
- Improved Oil Control and Reduced Aeration: Scavenge pumps rapidly remove oil from the crankcase. This minimizes oil sloshing and oil aeration (foaming). Aerated oil is less effective as a lubricant and coolant. Dry sump systems reduce aeration, maintaining oil's effectiveness.
- Lower Engine Center of Gravity (Potentially): By eliminating a deep oil sump at the bottom of the engine, a dry sump system can allow for a slightly lower engine mounting position within the chassis, improving the car's center of gravity and handling.
- Increased Engine Power (Slightly): Reduced oil in the crankcase minimizes "oil drag" on the rotating crankshaft and other engine components, slightly reducing friction and increasing engine power output.
-
Dry Sump System Components: Key components of an F1 dry sump system include:
- External Oil Tank: Often located low in the chassis for center of gravity benefits. Can be made of aluminum or composite materials.
- Pressure Pump: High-capacity, multi-stage pump to deliver oil at the required pressure.
- Scavenge Pump(s): Multiple pumps strategically positioned to scavenge oil from various points in the crankcase.
- Oil Lines and Hoses: Extensive network of lines to route oil between the tank, engine, pumps, and oil cooler.
- Oil Separator/Air-Oil Separator: To remove air from the scavenged oil before it returns to the oil tank, further reducing aeration.
Oil Types: Specialized Formulations for Extreme Demands
Formula 1 engines require highly specialized engine oils that are far beyond typical road car oils. These oils are formulated to withstand extreme temperatures, pressures, and shear forces, while providing optimal lubrication and cooling.
-
Key Properties of F1 Engine Oils:
- High Viscosity Index (VI): Viscosity index measures how much an oil's viscosity changes with temperature. F1 oils need a very high VI to maintain adequate viscosity at extremely high engine temperatures while still flowing readily at lower temperatures during engine start-up.
- High Thermal Stability: F1 oils must resist thermal breakdown and oxidation at very high temperatures to prevent sludge and deposit formation, which can compromise lubrication and cooling.
- High Shear Stability: Oils are subjected to immense shear forces in high-speed engine bearings and gearboxes. F1 oils are formulated to resist viscosity breakdown under these shear forces, maintaining consistent lubrication.
- Anti-Wear Additives: Advanced anti-wear additives are crucial to minimize friction and wear on engine components, especially under extreme loads and high RPMs. Common additives include ZDDP (Zinc dialkyldithiophosphate) and molybdenum compounds, although formulations are constantly evolving with newer technologies.
- Detergents and Dispersants: To keep engine components clean by preventing deposit formation and suspending contaminants.
- Friction Modifiers: To further reduce friction and improve engine efficiency.
- Anti-Foam Agents: To minimize oil foaming, particularly important in dry sump systems and at high RPMs.
-
Synthetic Base Oils: F1 engine oils are almost exclusively based on high-quality synthetic base oils (like PAOs - Polyalphaolefins, or Esters). Synthetic oils offer superior thermal stability, viscosity index, and oxidation resistance compared to conventional mineral oils.
-
Oil Viscosity Grades: F1 teams carefully select oil viscosity grades based on engine design, operating conditions, and ambient temperatures. They might use relatively low viscosity oils (e.g., 0W-20 or even lower) to minimize friction and maximize power, especially in qualifying, but may opt for slightly higher viscosity oils for longer races or hotter conditions to ensure robust lubrication and wear protection.
Oil Cooling: Dissipating Heat from Lubricant
Engine oil in F1 engines absorbs a significant amount of heat from engine components. Effective oil cooling is essential to prevent oil temperatures from exceeding critical limits and to maintain oil's lubricating properties.
-
Oil Radiator/Oil Cooler: F1 cars are equipped with dedicated oil radiators (or oil coolers). These are heat exchangers that transfer heat from the hot engine oil to the ambient air.
- Location: Oil radiators are often located within the sidepods, alongside or integrated with the water radiators. Placement is dictated by aerodynamic considerations and available airflow.
- Design: Similar to water radiators, oil radiators are designed for high efficiency, using fine fins and tubes to maximize heat transfer surface area within a compact volume.
- Airflow Management: Effective airflow through the oil radiator is crucial. Ducting and aerodynamic shaping are used to direct cooling air and vent hot air efficiently.
-
Oil-to-Water Heat Exchangers (Less Common for Primary Cooling): While air-to-oil radiators are the primary method, some F1 engines may also use small oil-to-water heat exchangers. These transfer heat from the oil to the engine coolant. This can be useful for quickly warming up oil during engine start-up or for fine-tuning oil temperature management, but air-to-oil radiators are the primary cooling method due to their greater cooling capacity.
-
Oil Temperature Control: Maintaining optimal oil temperature is critical. The engine management system monitors oil temperature via sensors and works to keep it within the ideal range. Excessively high oil temperatures can lead to oil breakdown, reduced lubrication effectiveness, and engine damage. Over-cooling the oil can also be detrimental, increasing viscosity and friction.
Oil Management Strategies: Monitoring and Optimization
Effective oil management in Formula 1 goes beyond just cooling and lubrication. It involves careful monitoring, strategic adjustments, and minimizing oil consumption.
-
Oil Pressure and Temperature Monitoring: F1 cars are equipped with numerous sensors to continuously monitor oil pressure and temperature at various points in the lubrication system. This data is transmitted in real-time via telemetry to the team's engineers in the pit lane.
- Real-time Analysis: Engineers constantly monitor oil pressure and temperature data to ensure the lubrication system is functioning correctly. Deviations from normal parameters can indicate potential problems.
- Driver Displays: Drivers also have oil pressure and temperature readouts on their steering wheel displays to be aware of lubrication system status.
-
Oil Consumption Management: While minimizing friction is a goal, some controlled oil consumption is often tolerated in high-performance engines as it can contribute to lubrication of piston rings and cylinder walls. However, excessive oil consumption is undesirable. F1 teams carefully manage oil consumption through:
- Piston Ring Design and Materials: Optimizing piston ring design and materials to minimize oil blow-by (oil passing into the combustion chamber) while maintaining effective cylinder sealing.
- Valve Stem Seals: High-quality valve stem seals to prevent oil leakage down valve guides.
- Engine Breathing and Crankcase Ventilation: Proper crankcase ventilation systems to manage pressure and prevent oil leaks.
- Oil Level Monitoring: Teams carefully monitor oil levels and may need to top up oil during long races, although refueling during races is no longer permitted, so initial oil fill must be sufficient.
-
Oil System Calibration and Optimization: The entire lubrication system is meticulously calibrated and optimized during engine development and testing. This includes:
- Oil Pump Capacity and Pressure Settings: Matching pump capacity to engine requirements and optimizing pressure relief valve settings.
- Oil Radiator Sizing and Airflow Ducting: Fine-tuning radiator size and ducting for optimal cooling performance without excessive aerodynamic penalty.
- Oil System Component Design: Optimizing the design of oil lines, fittings, and other components to minimize pressure losses and ensure efficient oil flow.